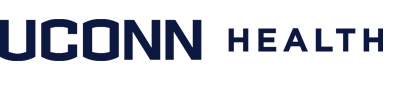
Office of Logistics Management
UCH CENTRAL WAREHOUE SERVICES
POLICIES & PROCEDURES

General:
The Procedures Contained Herein Describe the Internal
Central Warehouse Management Procedures. The same procedures are
also used in the Perioperative, IR and Hospital Inventory/PAR programs.
- The Central Warehouse stocks product that are frequently used; office PAR
stock, data processing, janitorial,
laboratory, dental and medical supplies which are used by more than one department, or are used on a repetitive basis by one department.
- The Central Warehouse uses the Logistics Management Information System to control stock at all levels,
including the Hospital, UMG and Dental PAR programs.
- Orders placed to the Central Warehouse are requisitioned using the
Logistics Management Web Ordering
e-Portal Navigator System.
Billing is also handled through this system.
- The Warehouse has been evaluated several times over the last several years
by independent consultants. All reports have shown the Warehouse as
very efficient and a state-of-the-art operation. The reports have also
shown that the Warehouse represented a major cost savings to the
University of Connecticut Health Center.
Approximately 90% of all medical product used by the Hospital and
Clinics can be found in the Central Warehouse formulary.
Catalog:
-
A complete warehouse catalog will be maintained in the Material Management
e-Portal Navigator System.
- The catalog will be updated once annually in the month of July.
- The
OLM Resource division will maintain and update the catalog on a regular basis as required.
Stock Items:
-
Stock items will be reviewed annually in April to determine retention for the coming year.
- Working together with the University Director of Logistics Management, the OLM
Logistics Manager and the Central Warehouse Supervisor shall approve all additions/removals.
Access Policy:
-
The Central Warehouse will be operated as a closed store, whereby, customers are excluded from the store area except on an
approved or escorted basis. As stated previously, orders can be placed through the Logistics Management
e-Portal navigator System.
Pricing Policy:
-
An average pricing principal is used when costing items.
Logical Unit Of Measure:
-
The unit of measure shall be the standard pack size used by the majority of departments.
- Items may be broken down to less than standard pack size, but should be kept to a minimum.
- Items such as forms may be established as a standard pack to facilitate easier delivery and inventory.
Damaged Goods Policy:
-
Damaged goods received from the vendor or returned from a department will be returned to the vendor for credit or
replacement.
Filling Orders:
The following applies to filling orders for the Central Warehouse:
-
Orders are generated by the user through the Logistics Management e-Portal
Navigator System.
- Two copies of requisitions (pick-tickets) will be printed by the Logistics Data Control
Administrative Program Assistant.
- The Storekeepers will fill the order and complete the requisition by indicating
that the order has been filled.
- Any discrepancies will be noted on the requisition. A copy of the requisition will be provided to the user and the second copy returned to the
Logistics Data Control Administrative Program Assistant for billing purposes.
Billing:
-
Billing for goods sold will be accomplished daily as they occur.
- Billing is automatically accomplished as the requisitions are issued in the
Logistics Management e-Portal Navigator System.
-
Payment Purposes Only (PPO): Product that is
brought in by a vendor or Physician and Logistics Management is notified after
the fact to have the product paid for or product that is received without
prior approval from Logistics Management or the VAT will be known as a PPO.
Inventory Control:
Inventory control shall be maintained by use of the Logistics Management e-Portal
Navigator System. The Warehouse Supervisor or
his/her designee shall maintain the system, control entries and make adjustments. The following procedures will be followed in
controlling the Central Warehouse Inventory.
- Central Warehouse items will be controlled by stock numbers assigned by the
Logistics Data Control Administrative Program Assistant.
-
Purchases of warehouse items will be entered into the Logistics Management
Information System by the Warehouse Supervisor as they occur.
- Adjustments to the Logistics Management Information System can be made to correct errors in posting, provide credits for returned goods and record damaged goods. Adjustments to compensate for overages/shortages will only be made with the approval of the Director of Logistics Management.
- Weekly Cycle Counts will be conducted by the Logistics
Supervisor and
Warehouse Materials Supervisor on not less than 20 warehouse items per week. Complete inventories will be conducted at the end of the fiscal year in the month of June. All
counts will be inspected by the Director and/or the Logistics Manager.
Inventory
& Replenishment Procedures:
PAR Inventory & Replenishment Process
- Daily inventory review and ordering
- PAR Replenishment
- Review of requisitioned items
- Weekly Cycle Count check
- Only original packaging is allowed in PAR/Supply
areas. Cardboard shipping containers are not allowed in any of the
PAR/Supply areas in the Hospital, UMG or Dental.
- Annual inventory performed in the month of June
Annual Inventory Procedures:
-
An inventory will be conducted annually during the month of June.
- The inventory will be supervised by the Logistics Manager and/or
Director.
- All inventory will be frozen at a pre-designated time and will remain frozen until released by the
Logistics Manager and/or
Director.
- Designated teams acting independently of each other will conduct the inventory. Both teams will use the
Inventory Count Form generated by the Logistics Management System to record their
count.
- Counts will be compared against the Logistics Management System by the OLM
Logistics Supervisor. If the two counts do not agree on a given item, then a recount of that item will be taken by the Warehouse Supervisor.
- Upon completion of the physical inventory, the Logistics Manager and/or
Director will complete a Stock Value List. The
Logistics Manager will certify that the report is true and accurate and submit the reports to the
University Director for Logistics Management.
- The
University Director for Logistics Management shall submit the report to
Finance.
REVISION LOG
Revision No. Description
- 10/03/2008
- 02/05/2009
- 07/29/2009
- 10/01/2013
- 09/11/2015
- 08/22/2023
- ----
- ----